Why Medical Device Startups Need to Build a Strong Quality Management System Foundation from Day One
Establishing a medical startup is a challenging and risky process. A lot of things can go wrong, particularly at the beginning. Hence, it is important for startups to pay close attention to the formation of their policies, procedures, and documentation, in order to minimise the chance of delays in your regulatory readiness for clinical trials and time to market. In order to do all of the above things successfully, startups must implement an effective QMS, or at least the foundation for a good QMS, from the very beginning.
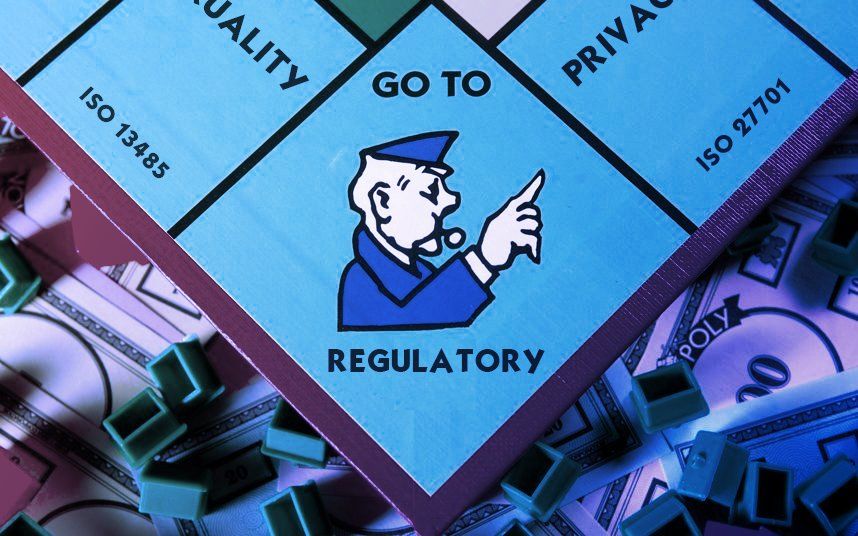
What is a Quality Management System (QMS)?
A Quality Management System is a formalised system that documents the relevant processes, procedures, and responsibilities for meeting the customer and regulatory requirements related to a product. This information applies to the initial delivery of the product, as well as any post-delivery activities, such as addressing customer feedback and complaints. The QMS focuses on ensuring continuous improvements in effectiveness and efficiency. In medical software development, this can include the execution of internal audits to identify areas of improvement, providing a baseline for training staff, and enabling corrective action for any problems that arise.
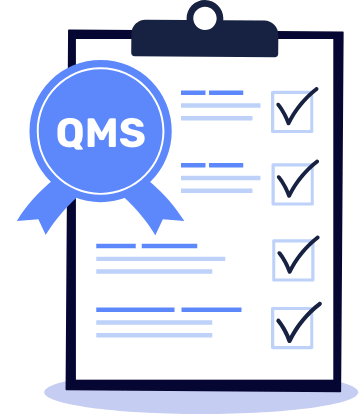
Quality Management Systems are more than just proper documentation. They are first and foremost there to guarantee the safety of people and the environment, and in the medical space, specifically the safety of the patients.
What are the regulatory foundations of a QMS?
There are two main ISO standards that are used as the basis for a QMS. These are ISO 13485, and ISO 9001. ISO 9001, which was last reviewed in 2021, is a generic standard that specifies QMS requirements for any type of organisation.
So when does ISO 13485 come into play?
ISO 13485 becomes relevant when dealing with medical devices. Published in 2016, it acts as a stringent QMS standard specifically for medical devices.
Having a compliant QMS is also one of the requirements under the EU Medical Device Regulations (MDR), which came into effect on 26 May 2021. All medical device manufacturers and distributors in the EU have to comply with the EU MDR, including those that produce self-certified Class I devices
The steps you, as a medical device startup, will probably need to take:
- First, you must form your multidisciplinary team. This should include some team members who are responsible for quality management, such as the Quality Manager. It is very important that employees with a thorough knowledge of Quality Management are involved in this process.
- Create a detailed plan for setting up the QMS. Identify which processes and procedures are needed, based on the relevant regulations, customer requirements, and any additional requirements defined by the organisation itself.
- Now, you can start constructing your QMS. Create detailed standard operating procedures (SOPs) for these processes and procedures. The system documentation must be created, including the organisational structure, the quality policy, the quality objects, risk management, and the manufacturing process, testing, and validation. You should also create a Design History File (DHF). These documents will form a process map for your organisation.
- Start implementing the processes and procedures. All employees that have to follow these processes and procedures must be trained on the SOPs. Make sure to collect feedback from the people who use them, and use this feedback to make changes if necessary. Any changes must be communicated to the relevant personnel.
- Execute the first internal audit. This is typically done by a third party. Any issues discovered during this internal audit should be used as the basis for any improvements.
- Next, a management review meeting should take place. This ensures that the top management are involved by evaluating the performance and adequacy of the QMS.
- An external body, notified body, or consultant then performs an external audit of your QMS. Any issues identified by the external audit can then be resolved.
- After all major issues have been addressed, the certification can be granted.
Even after certification, your QMS processes and procedures should be continually monitored, with improvements being made when necessary.
How a well-implemented QMS can be beneficial to medical device startups
A well-implemented QMS is hugely beneficial to any startup. As a QMS provides a strong foundation that directs and documents the startup’s activities, it helps tremendously with compliance, especially when achieving regulatory certifications. This is because a lot of the documentation needed to meet certain regulations is already available in the QMS. This saves valuable time and money - two things that can often be in short supply when establishing a startup.
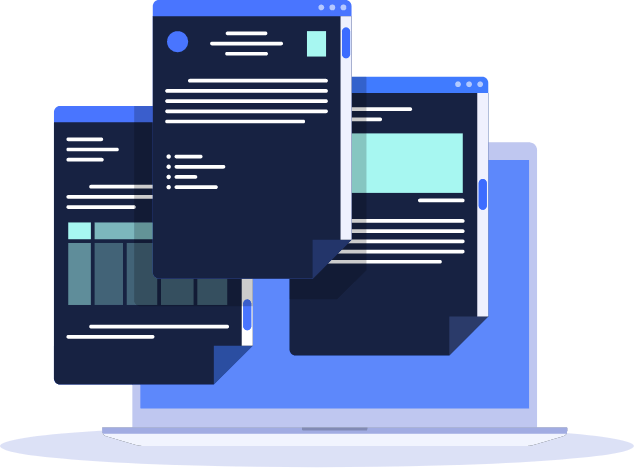
The QMS also provides a useful training baseline for current and new employees. This helps the management team remain accountable, as it makes sure that every employee hired has the appropriate skills and training, including a thorough knowledge of the startup’s procedures and processes. The QMS also helps eliminate unnecessary activities and closes gaps in performance, thus improving overall efficiency and saving precious time.
Why must startups start building the foundation of their QMS from day one?
Startups should establish a QMS as early as possible in their development process. Having detailed documentation about the processes of the business and why decisions were made is extremely important. When a startup is only just beginning their activities, the environment can be very rapid and unregulated, due to the high-risk and flexible nature of most startup environments. This can mean that the reasons for decisions can be lost or forgotten. The thorough documentation provided by a QMS means that this issue is avoided, and the product quality is not compromised as a result. In a startup space, this can secure the long-term existence of a company on the market, and ensure that the product is safe and reliable.
Not beginning to establish a QMS from early on can have a significant impact on your operations. This is because as development progresses, there is less time available to dedicate to forming a QMS, as other tasks will become a priority. Furthermore, startup teams can find it hard to adapt to new processes further down the line, as this can cause huge and difficult changes in the working culture. Thus, starting to build the QMS from day one saves having to play catch-up later in the development process, therefore saving time and keeping a consistent working culture. Establishing a QMS from the start will most certainly have its benefits down the line, especially during the auditing phases your company will go through.
You'll be happy to know that by building your solution on Extra Horizon as a certified supplier, large chunks of the Design and Manufacturing documentation will no longer be yours to worry about. To find out more, request a demonstration here, or have a look at our insights.
RECENT POSTS
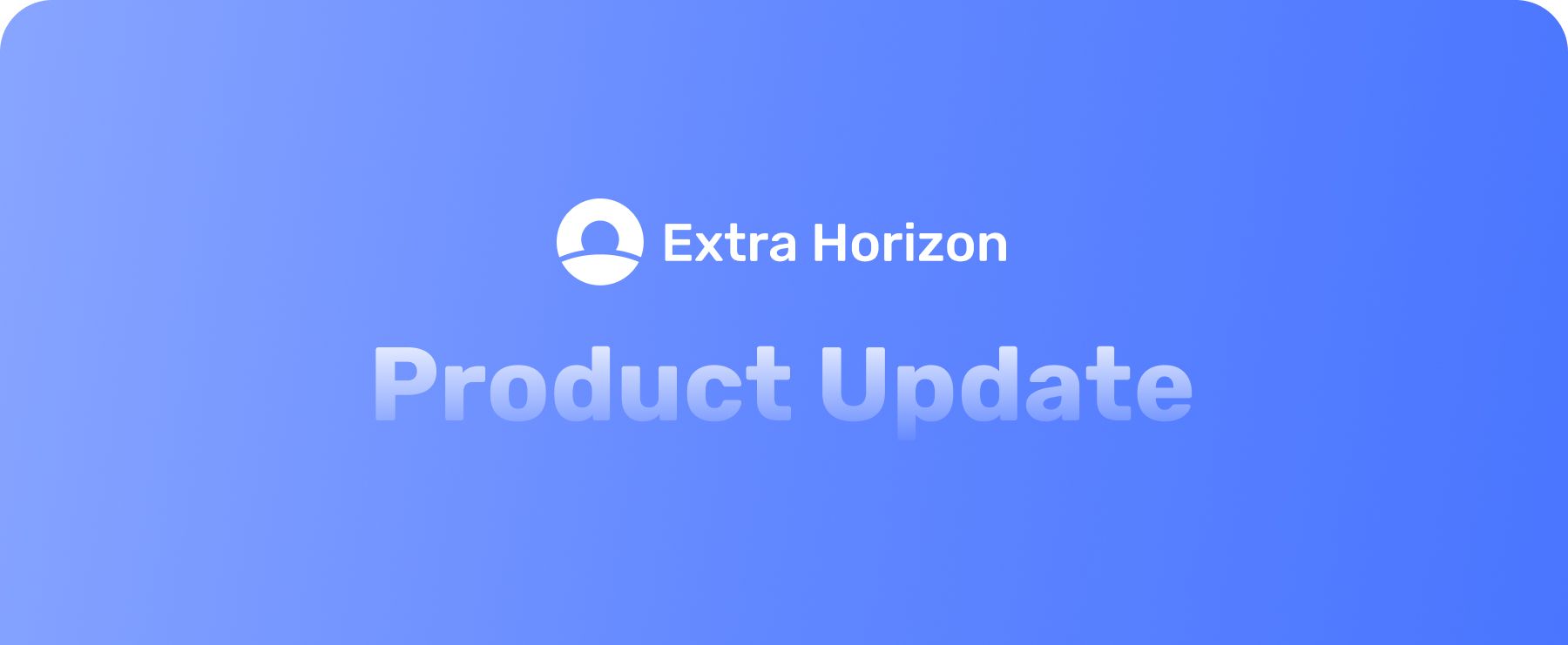
FREE EBOOKS
GOT QUESTIONS?